Introduction
Achieving compliant drug product labels is a challenge for pharmaceutical and biotech companies from large to small. Beyond the obvious critical risk to patient safety, noncompliant labels can result in regulatory action, fines, litigation, inefficiency through rework, negative brand impact, and product recalls.
Pharmaceutical and biotech companies have no option but to optimize their internal operations to ensure their operational excellence, compliance, accountability and traceability across end-to-end labeling to ensure patients are safe and regulatory requirements are met where their product is marketed.
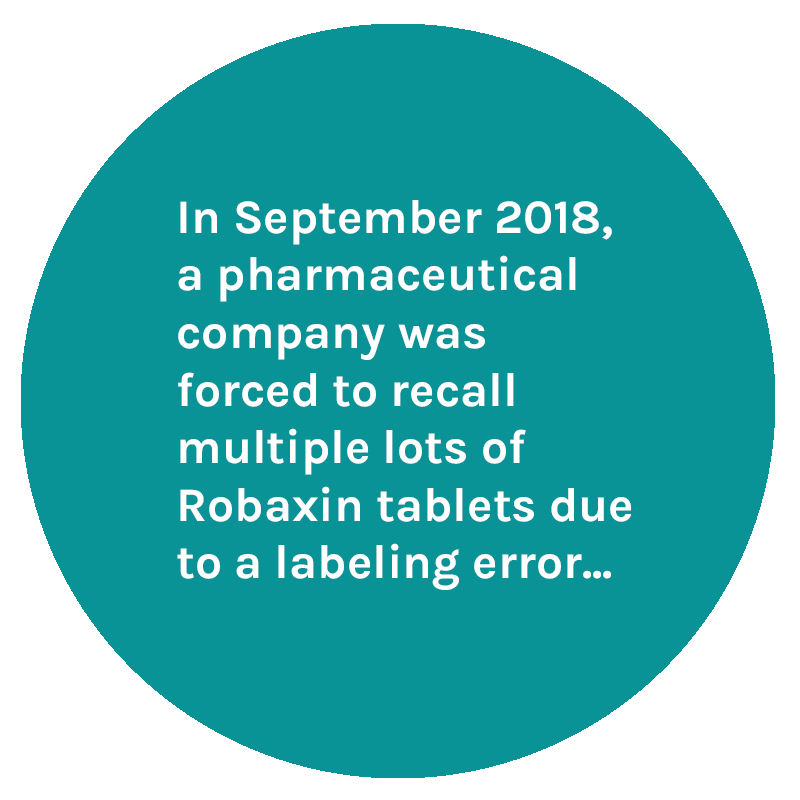
Case
In September 2018, a pharmaceutical company was forced to recall multiple lots of one of their drugs due to an error in the dosing information that appeared on the label.
This error is not unique to this particular pharmaceutical company. In fact, when looking across the life sciences industry, most companies do not have established processes that enable them to be compliant with their product labels.
How do errors like this happen? Many factors play a role. A limited set of examples is provided below:
- Working off of the wrong label version (uncontrolled version management)
- Misaligned content from company core data sheet to local label to artwork (fragmented processes)
- Suboptimal/lack of technology and multiple siloed systems (no single source of truth for label content)
16 Tablets or 6?
In September 2018, a pharmaceutical company was forced to recall multiple lots of Robaxin tablets due to a labeling error in the dosing information, which put patients at risk for overdosing, seizures, coma, or death. The correct dose was 2 tablets 3 times a day!
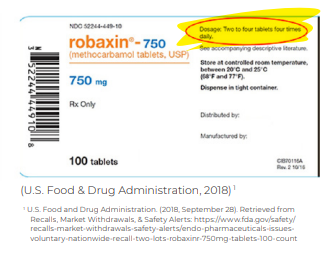
There are 3 key enterprise-level elements to taking a comprehensive approach for implementing an end-to-end (signal to patient) labeling program.
Three Key Elements to the Successful Implementation of an End-to-End Labeling Program
Operational Excellence:
Organizational structure fit for purpose
- OCM and training
Compliance:
End-to-end process, KPIs, and label alignment
Accountablity and Traceablity:
Label management with automated tracking and reporting
Operational Excellence
What Should a Labeling Organization Look Like?
While there is no one-size-fits-all answer to this question, there are multiple commonalities to an efficient and optimized labeling organization. The operating model for labeling should be appropriate for the size and complexity of the organization. What works for a small company focused on generics will not work for a Fortune 100 pharmaceutical focused on R&D of new products.
What Governance Structure Should be Considered for a Labeling Organization?
A centralized labeling function that owns and controls the end-to-end labeling process, KPIs, tracking, and reporting from signal confirmation to implementation in the packaging would be the ideal state. Typically, however, that is not the case, and, in most companies, the Company Core Data Sheet (CCDS) is managed in isolation of the local labels and the local labels are managed in isolation of artwork. This fragmented and siloed approach opens the organization up to significant risk of noncompliant labels.
Change Management: Ensuring a Positive and Collaborative Cross-Functional and Global Culture
Often the most difficult part of change is not the new software or process; it is the human element.
Some key considerations for organizational change management:
- Change management does not begin at the launch of a new process. It starts with the first awareness of the changes to come.
- It is critical to give the impacted staff a voice in any initiative that will address process development/optimization or technology implementation. This will reduce potential incidents of users saying, “They didn’t even ask us what we needed!”
- Communication with all stakeholders is a key success factor for change. Without building awareness and understanding, the user community will not know what is happening and when, and what it means for them. This poses a high risk for delayed launches and low adoption.
- “Turf awareness and sensitivity” is essential.
Use Case
For an organization transforming from a decentralized labeling function or a labeling function that is managed through the safety organization, to an organization that has a centralized labeling function, it will be necessary to be aware of the concerns functional areas may have with this shift in control. A properly constructed and implemented organizational change management plan that has buy-in and active sponsorship from senior leadership in the organization will reduce this type of fearful response from centralization of labeling.
Organizational Change Management
A key aspect of ensuring successful change is an understanding of the company’s culture and how to best introduce structural, process, or technology optimizations.
- Where are we today?
- Does the company culture value the importance and complexity of the change?
- How do we instill these values across all key stakeholders for successful change adoption?
- How do we empower our stakeholders to own and sustain the change through implementation?
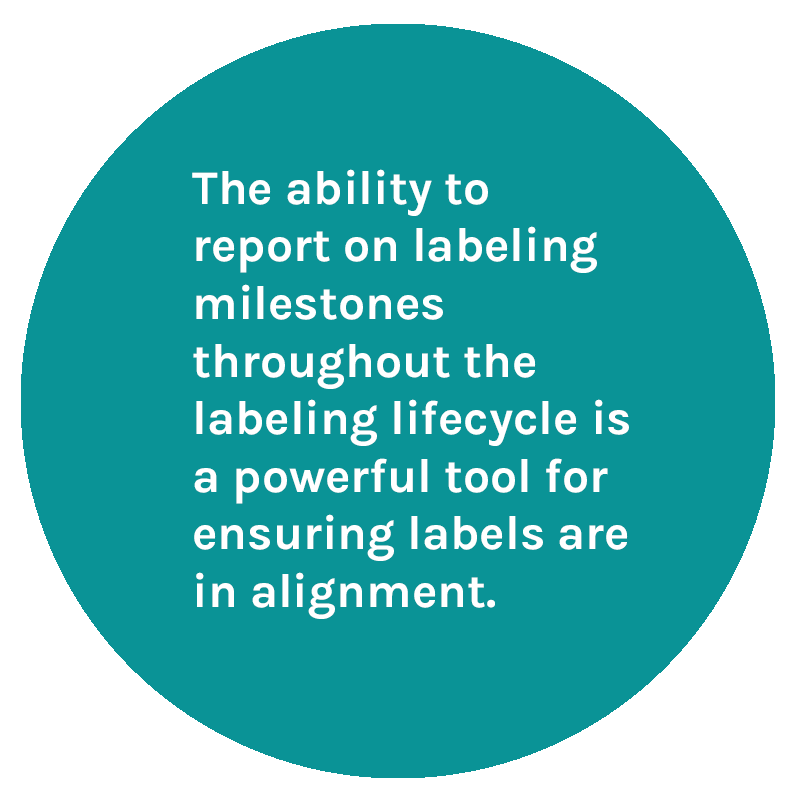
Compliance
What Does a Robust Process Ensure?
The concept of end-to-end labeling is one that encompasses the key stages of the labeling change process from label change confirmation (which includes safety signal confirmation and other triggers) through implementation of package updates and release. It stands to reason that an efficient and optimized end-to-end process should be in place to ensure the highest levels of compliance and traceability, but what this looks like can vary from organization to organization.
If the end-to-end global labeling process is considered from the creation, development, and maintenance of the Company Core Data Sheet (CCDS) (inclusive of the Company Core Safety Information (CCSI) to the management of each local product label, there are key objectives that can be applied across the industry, but the process needs to be tailored to address how an organization can feasibly take on these activities. All organizations should strive to establish a robust, documented, and cross-functionally adopted labeling process that aims to ensure that:
- Compliance is achieved across all labels
- CCDS and local labels are data-driven, well-written, and accurate
- Clear & accurate labeling content (safety and efficacy) is available and updated in a timely manner so that the product information can be disseminated correctly and effectively
- Label changes are monitored and tracked
- Scientific and medical information about the products is consistently conveyed in the various documents submitted to the Health Authority
- Responses to regional Health Authority inquiries regarding labeling are consistent with the company’s position
Why Quality Control, KPIs, Tracking, and Reporting Are Essential
It is also important for a robust process to include quality control checks at key stages to ensure alignment of local labels with source documents like a CCDS or reference label. Without careful and consistent quality control, there is a risk that safety updates will be improperly managed or misaligned within and across local labels. To enable quality control, a tracking mechanism, with well-defined KPIs and metrics, must be established to allow for traceability of labeling content throughout the lifecycle of the product. With transparency across the labels, it becomes possible to report on the history of a change arising from an internal or external trigger through to its implementation at the manufacturing site.
The Importance of Label Alignment
It is recommended that organizations undertake a label alignment effort if there is any doubt that their labels could be misaligned. This effort will ensure that all safety information in the CCDS for each product (as well as any country or regional variations) is reflected in all local labels.
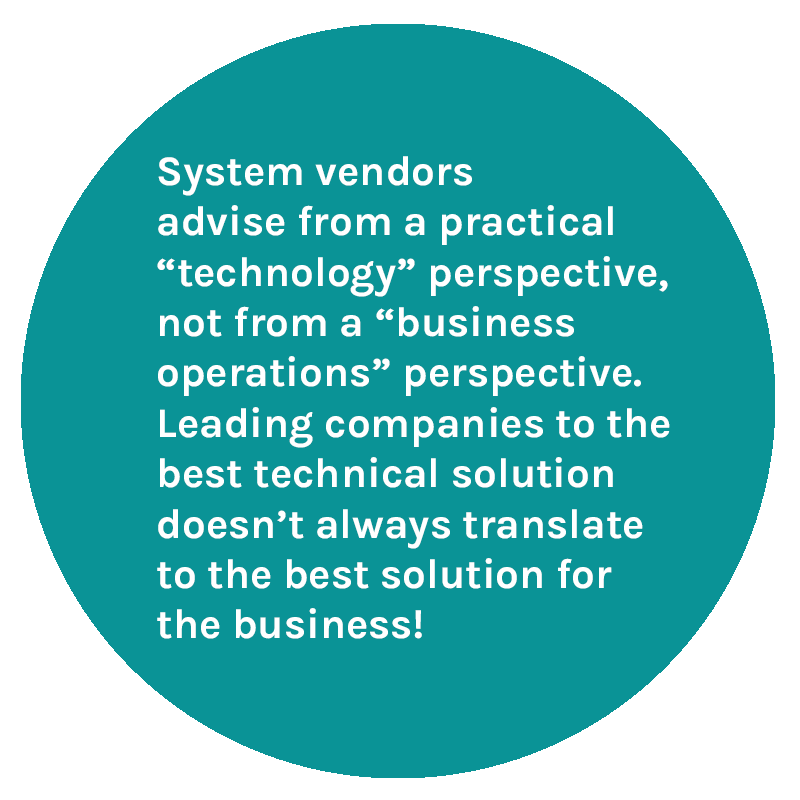
Comprehensive Training Is Central to Success
Labeling stakeholders in an organization need to be trained on any optimized labeling processes or systems. A comprehensive training program is detailed, interactive, and role based. This takes into account the different types of learners within an organization and addresses the user based on what role they will be performing in the system.
Technology
Technology Supports (Not Defines!) the Business Process
The global labeling process should not change when new technology is implemented. Technology should be used to make the process more efficient and streamlined and to allow for tracking and compliance. There are several Regulatory Information Management (RIM) systems available to support the document management needs of most organizations. The right RIM system will allow for storage of source documentation, submissions, and correspondence. Common capabilities include workflows that will at any point in time show where a label change is in the workflow as well as the ability to route labels for various content and quality control reviews before internal approval is given.
Most document management systems still fall short of giving labeling users the necessary tools to ensure the company remains in compliance.
- None of the systems enable tracking KPIs from signal confirmation to implementation in the packaging
- Few systems give the user the ability to create a Structured Product Labeling (SPL) file for electronic drug registration and listing data, which is a critical element of the labeling process.
- Many also lack the ability to perform branching, create label change plans, or track the implementation of content changes.
To truly be an end-to-end technology solution, a system, or suite of systems, needs to enable the business process from CCDS creation through artwork implementation at manufacturing sites. It is nearly impossible to find a RIM system that captures this full process. This has led to organizations relying on multiple systems in an attempt to meet all their business requirements. When these systems do not come from the same vendor, it becomes a challenge to seamlessly integrate the technology in order to support the needs of the optimized labeling process. Some companies have gone as far as creating a home-grown system to accommodate the deficiencies.
While a RIM system can be configured to fit the needs and requirements of the organization that will be utilizing it to achieve their document management and submission goals, it is likely lacking in labeling process functionality beyond the basic author, review, and approval workflows. Management of system configurations based on business needs can be a difficult and time-consuming process for one system, depending on the number of stakeholders involved and the complexity of the workflows and features that will be incorporated. Imagine the effort for multiple systems meant to work seamlessly together.
- While the vendor may configure their software for you, how do you know that it’s what is best for your organization?
- Will your vendor tell you about how their tool does not fit what you need?
- Will they understand your processes and technology well enough to ensure that ALL of your systems work together to support your business needs?
Author:
Justine Han, Managing Consultant Red Nucleus SS&A
jhan@rednucleus.com
Contributing Author:
Cheryl Silva Crawford, Compliance Manager Red Nucleus SS&A
csilva@rednucleus.com